As manufacturing continues to evolve in the digital age, the need to reskill and upgrade workers to meet today’s technological demands increases simultaneously. From robotics and automation jobs to data analytics and cybersecurity, the future of manufacturing depends on a workforce with new skills and knowledge. Let’s explore the importance of reskilling manufacturing workers for the digital age. We shall also know of how companies can support their employees to remain competitive in an ever-changing business environment. Join us as we explore and find out what it takes to thrive in today’s digitally-driven manufacturing environment.
Understanding the Need for Reskilling in the Manufacturing Industry
Manufacturing has been an important part of our global economy for centuries, providing vital goods and services to meet society’s needs. But with changes in technology and dynamic working conditions, the traditional manufacturing workforce is facing unprecedented challenges. The rise of digitization and automation has transformed the industry, widening the skills gap and threatening to replace many workers with automated machines.Â
Remaining competitive in today’s rapidly evolving manufacturing environment requires the adoption of new technologies and processes. This shift towards digitization requires highly skilled personnel, skilled in the use of complex machinery, understanding of data analysis, programming software, and advanced design processes. Unfortunately, many employees don’t have these skills or possess outdated skills that are no longer needed.
Consequently, there is now an urgent need to reskill the manufacturing sector to address this growing skills gap. Reskilling refers to providing existing employees with new skills or training in completely different areas to adapt to upcoming job roles. That includes equipping employees with the modern tools and techniques needed to use advanced equipment effectively.
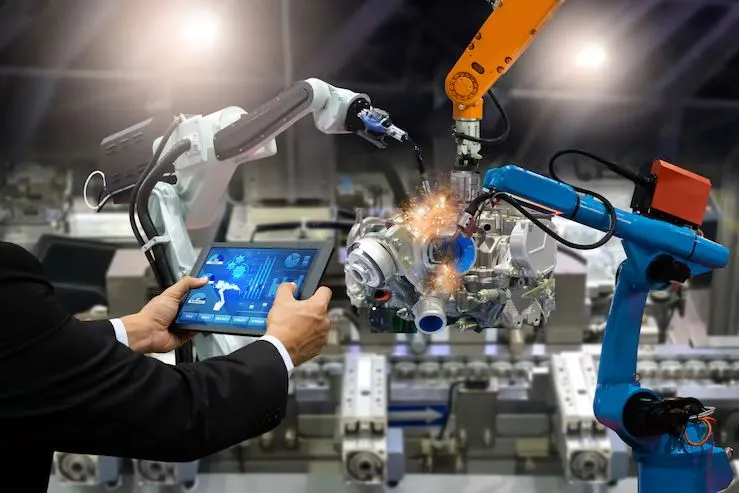
One of the reasons for this greater need for reskilling is automation. Many businesses are willing to automate processes traditionally performed by human workers, so only few jobs require manual labor. This trend poses a serious threat not only to individual factory workers but also to communities as a whole whose economies depend heavily on manufacturing industries.
Additionally, technological advancements continue at a rapid pace, resulting in ever-changing manufacturing processes. Entrepreneurs who fail to keep pace with these changes may follow their competitors, which ultimately results in business failure or loss of business.
Another important factor that gives rise to the important role of skill recovery in the industry is demographics. As older generations retire from their long-term corporate positions and leave vacancies – especially in more skilled roles – there are fewer candidates to fill these positions. This shortage of skilled workers underscores the need to reskill and train current employees to perform these jobs.
The ability of companies to re-skill manufacturing workforce is important not only for success but also for maintaining a strong economy. It is also for employees to have job security. It is important for manufacturers to invest their money to equip their workforce by providing training and education programs to keep pace with technological advances and keep up with advanced job demands. Skills will not only help bridge the gap but also drive change effectively in the digital age, creating a more sustainable future for businesses and their employees.
Challenges Faced by Employers in Reskilling Workers
The industry is constantly evolving, and with increasing technology and automation, the need for skilled workers who can adapt to these changes is increasing. This presents a number of challenges to employers when it comes to reskilling their workforce. Let’s discuss the key challenges employers face in reskilling employees for the digital age.
Lack of Awareness and Interest
One of the major challenges in redirecting the skills of the manufacturing workforce to the digital age is an unskilled and dissatisfied workforce. Many traditional manufacturing workers may not be aware of the changes taking place and the need for new skills to keep pace with technological advances. Furthermore, even if they are aware, they may not be interested in learning new skills for a variety of reasons, including fear of change, job security concerns, or lack of motivation.Â
A contributing factor to this lack of awareness is the limited use of digital technologies by traditional manufacturers. These workers are used to manual and physical work environments, where their responsibilities revolve around operating machinery and assembling materials. They consequently do not understand how these tasks are evolving with automation and digitization and understanding how their role in it is changing.
Furthermore, this perception, which has led to the stigmatization of professional jobs as less valuable or prestigious compared to professional jobs, can lead to a lack of interest in career advancement and growth opportunities in the manufacturing sector. Due to misconceptions about repetitive and multiskilled office jobs, many employees don’t see opportunities or high-paying roles in this field
Another reason for this gap in awareness and enthusiasm is the lack of adequate communication with employers about the technological changes taking place in their workplaces. Companies tend to focus on product development rather than spending time and resources on educating employees with new technology or providing training programs. This creates a perceived link between employees’ current skills and what will be expected of them in the future.Â
Budget Constraints
Budget constraints can often be a major obstacle when it comes to reskilling manufacturing workers for the digital age. The acquisition of new skills and the implementation of new technologies may require significant investment in the process, which may not always be feasible for all firms, especially small firms with limited resources
One way to deal with a financial crisis is to plan carefully and prioritize. This involves identifying key areas of expertise that need to be redesigned or upgraded to keep pace with changing trends and technologies. By focusing on these areas, companies can allocate their resources more efficiently and effectively.
Another way is to find cost-effective ways to reskill. This may also include the use of online training programs, which offer a wider range of courses at a lower cost than traditional in-person training programs. Companies may also seek partnerships with local community colleges or vocational schools offering less specialized training programs.
The use of certain products and services in manufacturing operations can also help reduce costs in the long run. This can free up resources that can then be applied to new skills programs.
Budget constraints should not prevent companies from investing in developing their employees for the digital age. One solution is to partner with government agencies or nonprofit organizations to provide grants or special grants for reskilling programs. These fellowships not only help alleviate the financial burden but also provide access to experienced faculty and industry insights.
Resistance to Change
Resistance to change is a common challenge when it comes to implementing new technologies and processes in the construction industry. Change can be confusing, and many employees may be hesitant or even resistant to adopting new policies or new skills. But in today’s digital age, manufacturers need to tackle this resistance head-on and understand the root causes so they can reclaim their workforce.
One of the main reasons for resistance to product change is the fear of job loss. Many employees believe that automation and digitization will make their jobs redundant and unemployable. This fear can cause employees to resist learning new skills or adapting to new technology, as they see it as a threat rather than an opportunity for growth.
Another source of resistance is a lack of understanding of the value of reskilling. Employees don’t realize how learning new skills or using new technology can actually improve their productivity and increase job satisfaction. Without clear communication about the positive impact of these changes on both the individual and the company, employees may find reskilling tedious or unnecessary.
Additionally, some employees may be concerned about their ability to learn new skills at some point in their lives. They think they are too old or lack sufficient knowledge or experience with the technology to adapt effectively. This makes them feel inadequate and insecure, further reinforcing resistance to change.
So, how can manufacturers deal with this resistance? First, corporate leaders must communicate effectively with their employees about the benefits of embracing digital and new skills opportunities. Clear communication channels must be established so that all employees understand why the changes are being made and how they will be positively impacted.
In addition, employers should provide training and support to help employees work harder. This could include allowing employees time to learn new skills during work hours, providing financial incentives or bonuses for successful completion of training programs, and creating a supportive environment for learning.
Solutions to Overcome Challenges and Successfully Reskill the Workforce
Reskilling the manufacturing workforce is essential to adapt to technological advances and remain competitive. Here are the basic solutions to overcome the challenges and ensure you regain successful skills:
- Industry partnerships: Partner with industry leaders and educational institutions to develop appropriate training programs. These networks can provide insight into critical skills and ensure that the curriculum is aligned with industry standards.
- On-the-job training: Implemented on-the-job training programs that enabled employees to learn new skills while performing their current roles. This approach minimizes the problem and provides a practical, hands-on experience.
- Flexible learning options: Offer flexible learning options such as online courses, evening classes, and modular training programmes. This flexibility allows employees to regain skills without leaving their current job.
- Government support and incentives:Â Seek government support and implement incentives for professional development. Subsidies, tax credits, and subsidies can reduce the financial burden on companies investing in reskilling programs.
- Employee engagement: Engage employees in reskilling by clearly communicating benefits and opportunities. Encourage a culture of continuous learning and provide career development support to motivate employees.
- Use of technology: Use advanced technologies like virtual reality (VR) and augmented reality (AR) for immersive training experiences. This technology can simulate real-world situations, making the learning process more effective.
Examples of Successful Manufacturing Workforce Undergoing Change
In recent years, the manufacturing process has undergone significant changes due to technological advances. This shift towards automation and digitization has increased the demand for workers with specialized skills relevant to the digital age, and as a result, many manufacturing companies have taken up the challenge of recovering the skills of their workers to compete in today’s rapidly changing marketplace
Let’s look at some successful examples of reskilling programs implemented by leading manufacturers:
- General Electric (GE): GE has been at the forefront of innovating its manufacturing workforce over the past few years. In 2017, they launched “Brilliant Learning,” an in-house program that gives employees access to online courses in areas such as data analytics, robotics, and advanced technology.
- Siemens: Siemens, the new global leader in industrial automation, has invested heavily in re-skilling its employees through various programs and partnerships. In addition to the introduction of their “Digital Academy”, an in-house facility that offers training courses on Industry 4.0 technologies such as artificial intelligence, cloud computing and cybersecurity, Siemens works closely with technical schools and trade unions to provide hands-on training for their employees.
- Schneider Electric: Known for its innovative energy management solutions, Schneider Electric understands the importance of keeping up with technological advancements to stay ahead of the competition. The company has launched its own “Digital Academy,” where employees can enhance their skills in areas such as data analytics, coding, and cybersecurity through immersive learning experiences
- Honeywell: Honeywell is another example of a manufacturer that has been able to re-skill its workforce in order to adapt to the changing technology. The company has created its own “Honeywell University” that offers certification programs and online courses in smart workplace technologies such as the Industrial Internet of Things (IIoT) and advanced manufacturing processes.
- Toyota: The multinational automaker has pioneered the application of simple principles and continuous improvement practices in its product development In recent years, Toyota has also recognized the importance of regaining its’ professional skills for the digital age. They have established “Toyota Motor North America University,” which gives their employees the opportunity to learn about new technologies and processes through hands-on training, online classes and curricula
These examples highlight the success that can be achieved by investing in reskilling in manufacturing industries. By equipping their employees with essential digital skills, these companies are not only ensuring they can compete but also contributing to a stronger and better-prepared workforce for the future.
Read More: